POWER SYSTEM CONSTRUCTION
Power System Components:
- Aluminum Driving Rod
- 5/8" Ball Screw
- 15/16"-6 Ball Nut
- Makita XDT08 Impact Driver
- 7/16" Hex Adapter
- Thrust Bearing
- Ball Nut Guide
- Composite Bushings
- Driving Rod Insert
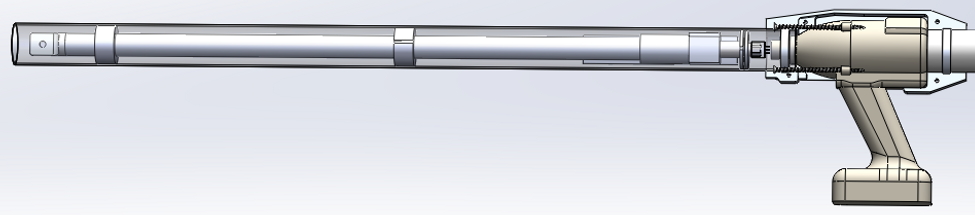
Ball Nut Guide (Rapid Prototype)
Makita XDT08
7/16" Nut Driver Adapter
Composite Bushings
Ball Nut
Ball screw
Driving Rod & Al. Adapter
Driving Rod Insert
Driving Rod Insert:
The aluminum driving rod insert was manufactured using a manual lathe and Bridgeport milling machine. A resin expoxy was then used to fasten the insert inside the aluminum driving rod. A surface plate and a series of squares were used to ensure the side face of the insert was parrellel with the side face of the ball when being glued in. If it were not straight, twisting and stresses would have been added to the linear action.
Composite Bushings:
The composite bushings used in the power system are Ultra-Comp 200 graphite-impregnated bushings. These were machined for free and donated by Kevin Smith of Tristar Composites. Kevin is amazing.
Ball Nut Guide:
The interior ball nut guide which restricts the twisting motion of the ball nut as the system is providing linear thrust was rapid-prototyped at Hogue technology building. DP420 3M Resin Epoxy was used to glue the guide inside the housing tube. The tube was indexed inside the tube using measured-out peices of bar and round stock.
Ball Nut & Screw:
The ball nut and ball screw were ordered from McMaster-Carr. Althought the large lead of the ball screw provides and excellent cutting cycle time, 1.65 seconds, the ball screw is heavier than other appropiate options. However, this ball screw was wildly more affordable, so it was the winner.
Aluminum Driving Rod & Adapter:
The driving rod was cut and faced to the required OAL using a chop saw and a manual lathe. The adapter was also machined on a lathe and then it was welded to the driving rod by lab technician, Trevor Reher. After the two components were welded together, ID threads were machined in the ID of the adapter to recieve the male threads of the ball nut. This is how the driving rod is fastened to the ball nut. The thrust is tranferred through the threads. The driving rod does not twist out of the threads thanks to the ball nut guide.
WELLINGTON & CO.
In collaboration with H.F. Hauff Co. Inc.